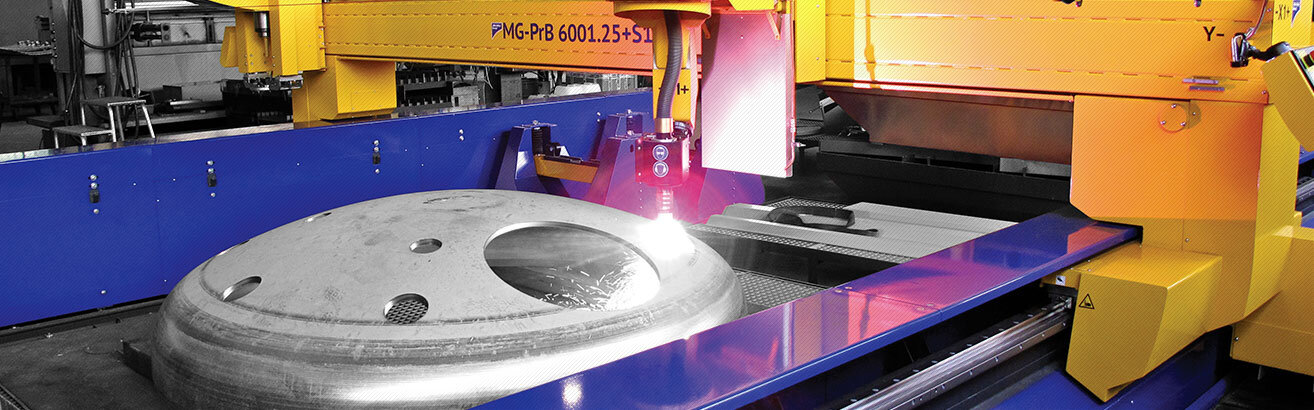
Dome processing
The cutting of 3D objects is an essential part of the manufacturing process in the production of pressure vessels and boilers counts. With this in mind, it is important that the cutting is carried out quickly and to a high quality - because only with accurate results will there be no need for time-consuming mechanical or manual post-processing. A typical cutting task in the area of dome processing is, for example, the cutting of openings for welding inlet pipes. The weld seam preparations required for this must meet the requirements of the subsequent welding task - this is exactly what MicroStep's fully automated process ensures.
MicroStep has developed the "Pantograph" plasma rotator for processing domes, which allows the torch tip to be tilted by up to 120°. At the same time, the pantograph has an exceptionally large Z-axis stroke, which allows the entire surface of the semi-finished product to be processed, even with particularly high domes. In addition, a revolutionary technology for unprecedented quality in dome processing has been available since 2016: With mScan, exact contours and high-precision bevel cuts are now standard for domes. The exact 3D geometries of the dome are recorded using a laser scanner. Based on the recorded contour parameters, mScan then determines the deviations from the ideal contour and thus enables optimized positioning of the cutting paths and, as a result, very high precision.
The implementation of this 3D scanning technology has contributed significantly to increasing the accuracy of the dome cutting process. This is because the actual dimension of a dome is subject to a certain tolerance - this means that the actual and ideal dimensions of a dome sometimes differ by several centimeters. Conventional methods of position correction, for example by controlling the plasma arc voltage, are therefore not applicable to 3D cutting. The implementation of a scanner also makes it possible to create an exact 3D model of the actual dome surface. This can then be used to fundamentally analyze the shape of the dome, identify its center point or define the optimal process sequence. But how does this work in detail?
During the scanning process, the iMSNC control system receives data from the scanner and pairs it with the positions of all the machine's movement axes at all times. The measurement data is then further refined: by applying displacement corrections to certain axis positions (based on the exact measurement of the machine kinematics with a laser interferometer) and by the calibration data of the bevel head and the 3D scanner itself (obtained via MicroStep's patented automatic calibration station ACTG).
High quality and great time savings when processing domes with many openings and weld preparations
This provides the control system with information about the exact position of the scanned object in relation to the cutting tool, enabling the object to be precisely located within the coordinate system of the respective cutting system. The scanner uses mSCAN to create a detailed surface representation (3D model) of the object in the form of a point cloud. In this way, the actual parameters of the dome can be fully described - including all deviations from the ideal shape.
MicroStep's 3D CAM software mCAM is then used to map the originally generated cutting path (i.e. the ideal cutting path created for the ideal shape of the object based on the STEP model) onto the real, scanned object - a new cutting plan is then created on this basis, taking into account the actual shape of the scanned object. All the automatic processes described are displayed to the operator in a user-friendly way in the form of 3D visualizations on the control system screen. Depending on the dome size, the entire process, which is carried out before the actual cutting, takes two to ten minutes.
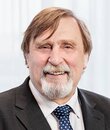
Head of R&D department
MicroStep
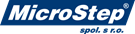
"With the mScan technology, we achieve unprecedented precision when cutting domes"
Of course, there are also cases in which it is not necessary to carry out the entire process - so depending on the task, the time required can be significantly reduced. For example, if the customer only wants to determine the dimensions of the dome. It is then sufficient to scan a "cross" that has previously been marked on the dome. In this way, at least the exact position of the semi-finished product is determined, which may be completely sufficient for the subsequent production steps. Incidentally, the top of the dome can be marked directly with a marking head or with a plasma torch, depending on the machine configuration. If the cutting plan only concerns part of the dome surface - e.g. the spherical upper part, which is normally quite flat - it may also not be necessary to scan the entire base: This is because when cutting in the area of the flatter, upper part, height control during cutting can also be based on the plasma arc voltage, which is a standard feature of every MicroStep plasma cutting machine.
All processes and 3D scanning functions can be accessed either directly by the machine operator on site or via a company network. In addition, as already described, mScan provides an exact analysis of the shape geometry - i.e. a comparison of the actual and ideal shapes of the scanned object. This alone is a powerful tool, for example for quality control in the production of 3D objects such as domes.
Thanks to the modular design of MicroStep machines, they can be configured according to the customer's exact requirements: This applies both in terms of desired dimensions and cutting ranges as well as configuration with desired processing technologies. For example, a gantry with a chamfering unit, a 3D scanner and a marker can be used to process both domes and sheet metal. This is the case with the DRM machine for Slawinski GmbH in Germany with an area for processing sheet metal with a surface area of 14,000 x 6,000 mm and domes with a diameter of 500 - 5,500 mm and a height of up to 1,200 mm.
MicroStep's mScan technology enables maximum precision in dome processing. A laser scanner integrated into the gantry determines the actual 3D surface geometry of the workpiece in advance.