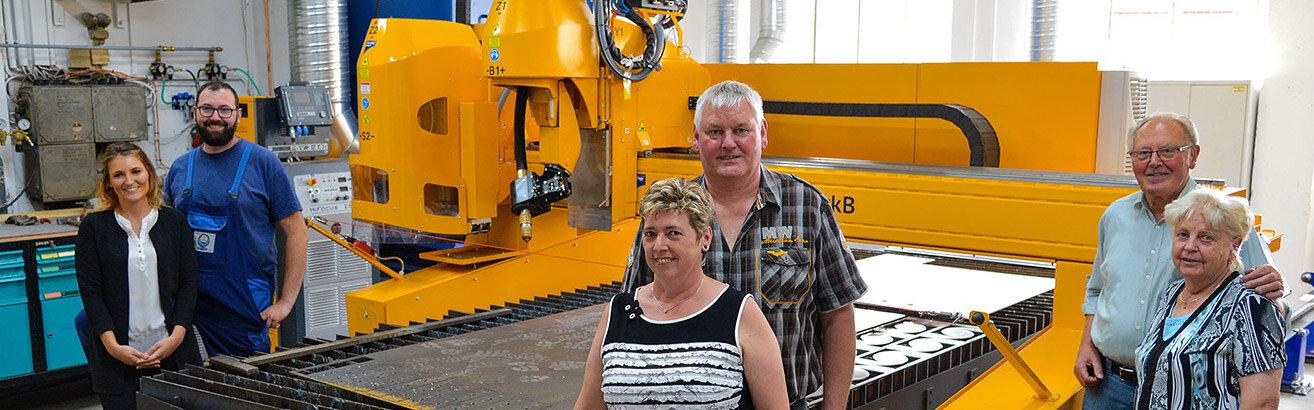
One company, three generations: The company Behrendt invests in a CombiCut with many options
"Standing out from the surrounding" with new configuration
Powerful, robust, modern and space-saving: these were the criteria that the Behrendt family business was looking for in its first cutting solution and came across in the CombiCut series from MicroStep – including bevel rotator and boring mill.
Published 02.06.2021 | Erich Wörishofer
Company profile:
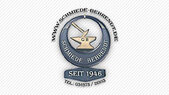
Rudolf-Breitscheid-Straße 2906386 OsternienburgGermany
The family-owned company Schmiede & Bauschlosserei Behrendt, located in Saxony-Anhalt/Germany, specializes primarily in the fields of blacksmithery and metal construction. Their product portfolio includes, for example, the manufacture of stairs, doors and gates, but also steel structures and grilles.
"The beveling unit and the good cutting quality tipped the scales in favor of MicroStep," says Chris Behrendt. His family business opted for a drilling plasma cutting system with rotator for beveling up to 45°.
When it comes to small series and individual production, the company Schmiede & Bauschlosserei Behrendt is in demand around Osternienburg in the south of Magdeburg in Germany. The portfolio includes construction, manufacturing but also assembly thanks to a 19-strong team. In order to be able to produce more flexibly and faster, the family business invested in the field of cutting. After an intensive search and a thorough examination of the market, the Behrendt family decided on a combined drilling-plasma cutting machine from MicroStep because of "the cutting quality and the endless rotating bevel tool".
In the heart of the Schmiede & Bauschlosserei Behrendt in Germany, the fire still burns in the furnace. The former blacksmith's shop, which was founded around 1900, developed into a family business that is widely known for its staircase construction, wrought-iron grilles, gates and doors and knows how to combine traditional craftsmanship with modern service. For more than 70 years, the business has been firmly in the hands of the Behrendt family. Karl Behrendt made the beginning, with Karl-Heinz, Göran and Chris today three generations including women are active, the next generation is already dashing through the halls of the approximately 1,000 square meters of factory space.
Many satisfied customers because of on-time delivery and consistent quality
The punctuality and quality of the work are in demand not only in Osternienburg, between Leipzig and Magdeburg - from prefabricated construction companies, medium-sized companies and private individuals alike. "We are available for big things but also work for smaller companies. We can react quickly from 0 to 100. Due to our adherence to deadlines and suitable results, we count many satisfied customers. Customers appreciate our efficiency," says owner Göran Behrendt, explaining the strengths of the 19-employee training company, which specializes primarily in the production of small and very small series.
Up to 30 times faster with new solution
Behind the company lies a year of modernization – after all, the machinery was expanded to include the field of cutting - including an overhead crane for easy loading. The Schmiede & Bauschlosserei Behrendt invested in a combined drilling-plasma cutting system of the CombiCut series from MicroStep for cutting contours and bevels but also for drilling, countersinking and tapping on sheet metal. The company received support from the European Regional Development Fund (ERDF) – and the new acquisition quickly paid for itself since it was put into operation in mid-2018. "We save a lot of time with beveling, countersinking, slot drilling or marking. Depending on the component, we are 30 times faster than before, when we did a lot of manual production (with band saw, grinding machine, punching device, editor's note)," says machine operator and next scion of the family, Chris Behrendt.
Looking for a compact system with a high degree of flexibility
It was he who pushed for an investment in 2016. The response time was to be improved, the reproducibility of the components increased, the work steps automated; all in order to be able to better absorb bottlenecks, to be more independent of contract cutters and to be able to deliver high-quality results more easily. "The system should be powerful, robust, modern and space-saving. Our space is limited. Flexibility was particularly important to us, so that we could do several processing steps with one system," Göran Behrendt looks back. So the two looked around at EuroBLECH 2016 and were enthusiastic about the solutions offered by modern system types. During a demonstration at the Kjellberg Technology Center in Finsterwalde afterwards, the focus ultimately fell on MicroStep because of the compact design of the MasterCut Compact on display – after all, the Behrendts were originally looking for a 2D plasma cutting system.
"We save a lot of time with beveling, countersinking, slot drilling or marking. Depending on the component, we are 30 times faster than before, when we did a lot of manual production"
Chris Behrendt,
Owner family | Schmiede & Bauschlosserei Behrendt
Machine profile:
CombiCut series- Working area 4,500 x 2,000 mm
- Plasma rotator for weld preparation up to 45° with autocalibration
feature (ACTG®) - Drilling up to Ø 40 mm and tapping up to M33
Closing market gaps in the region with investments
As the possibilities of modern cutting systems grew, so did the scope of equipment of the desired system type. After an intensive analysis of several suppliers in combination with the preferred Kjellberg technology, the two entrepreneurs decided on a gantry cutting system from MicroStep. The Behrendt company invested in the CombiCut series with rotator, drilling support and powerful 280i neo plasma source from Kjellberg. "The bevel unit and the good cutting quality tipped the scales in favor of MicroStep. With the configuration, we wanted to stand out in the surrounding area: we looked to see what market gaps existed in the region. We have a large demand for drilling, and we need the rotator a lot for weld beveling," says Chris Behrendt. The Kjellberg plasma system was deliberately chosen in order to be able to process medium material thicknesses to a high standard. Although 10 to 25 mm structural steel is mostly cut, 35 mm thick flat material as well as stainless steel plates have also been processed. Thanks to the new possibilities, the Behrendt company also offers contract work, and the first projects have been completed successfully and to full customer satisfaction.
New acquisition has paid off: "We are now faster and more flexible"
Even after six months of single-shift operation, the conclusion is positive: "The consulting was good, the project department invested a lot of time and worked intensively to ensure that everything fit exactly. We are very satisfied," says Göran Behrendt. For son Chris, first man on the plasma drilling system, expectations have also been fully met. "The user training at MicroStep was excellent for getting started." There is a lot of documentation, he says, and one can always call the service department for support. By remote maintenance and video, they are quick to respond, he says. "Thanks to the training, it's easy to use. The process itself runs smoothly. We are now faster and more flexible."
OVERVIEW OF THE HIGHLIGHTS OF THE PLASMA CUTTING MACHINE COMBICUT 4501.20PRKB
CombiCut series for 3D processing on a working area of 4,500 x 2,000 mm
Schmiede & Bauschlosserei Behrendt opted for the CombiCut series, a robust and precise CNC guiding machine in gantry design, which was specially developed for continuous use in fine plasma cutting, among other things. Tailor-made to the customer's requirements, it was equipped with a oxyfuel cutting table with energy-saving section extraction and a working area of 4,500 x 2,000 mm. A ZPF 6H from Teka is used as filter system.
Bevel cutting up to 45° with the endless rotating MicroStep plasma rotator
The family-owned company relies on a system configuration with MicroStep plasma rotator for bevel cutting, for example, for weld edge preparation up to 45°. The automatic, patented ACTG® calibration unit ensures permanently precise cuts and exact repeatability of the work steps. The endless rotating bevel tool is connected to a HiFocus 280i neo plasma source with automatic gas console and Contour Cut Speed technology from the German manufacturer Kjellberg.
Drilling spindle for drilling up to 40 mm Ø and tapping up to M33
A 26.8 kW drilling spindle for drilling, countersinking and tapping has been integrated in the plasma cutting system to handle machining tasks on flat material. This powerful system allows drilling holes up to 40 mm Ø and tapping up to M33. The system was equipped with the ACDB (Automatic Calibration of Drill Bits) option, which enables consistently high-quality results and avoids errors through the automated and precise measurement of the drilling tools.
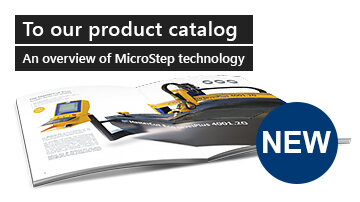
EXPERIENCE OUR SYSTEMS LIVE
in the CompetenceCenter South or North
- All four cutting technologies (laser, plasma, oxyfuel, waterjet)
- Innovative automation systems
- The latest solutions for bending and deburring
- Industry 4.0 demo factory
- Easy to reach: in the south and north of Germany
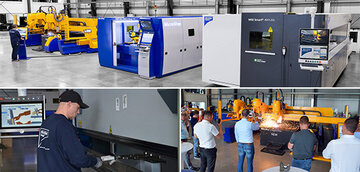