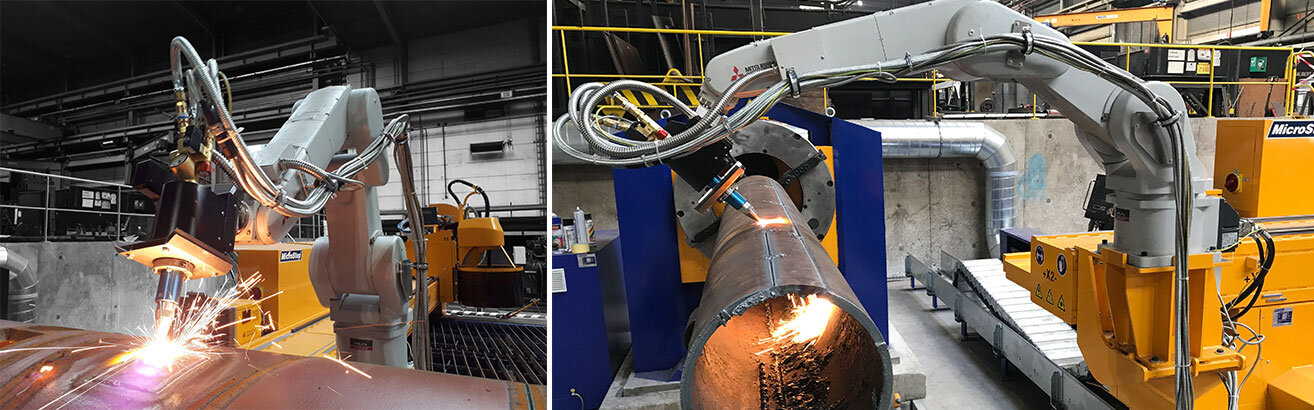
A robot attached to the portal of the plasma cutting machine enables the processing of pipes with extraordinary dimensions
Pipe cutting with robot technology from MicroStep
More flexibility for Jan De Nul Group with an exceptional plasma-oxyfuel cutting machine: An innovative combination of cutting machine and robot technology for processing sheet metal and pipes
Published 20.02.2019 | Erich Wörishofer
Company profile:
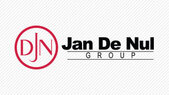
Tragel 609308 Hofstade-AalstBelgium
Jan De Nul Group is a leading expert in dredging and marine construction activities, as well as in specialized services
for the offshore industry of oil, gas and renewable energy. These core marine activities are further enhanced by Jan De
Nul Group’s in-house civil and environmental capabilities offering clients a complete package solution.
Machine profile:
MG series + Robot- Working area 12,000 x 3,000 mm
- Cutting of pipes Ø 100 – 2,000 mm up to a length of 12,000 mm
- Plasma rotator for weld preparation up to 50° with auto
calibration feature (ACTG®) - 2D oxyfuel
- Robotic arm with oxyfuel technology for bevel cutting of pipes
- Laser scanner for measuring of the real shape of pipe
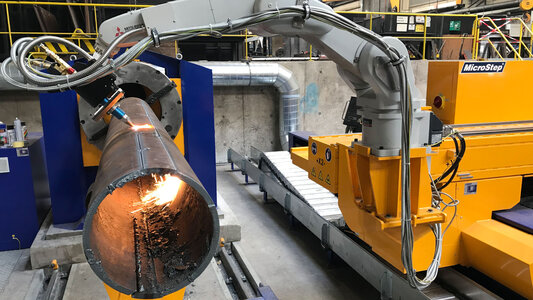
A robot arm equipped with an oxy-fuel torch is mounted on the outside of the cutting portal and can process pipes up to Ø 2,000 mm and with wall thicknesses of up to 80 mm.
A robotic arm on a gantry-type CNC plasma and oxyfuel cutting machine capable of cutting both flat plates and pipes with the same gantry? Even if it’s not the first of its kind in the lands of Benelux and beyond, it is still an exceptional and highly innovative combination of high-quality cutting technology. For MicroStep, this newly developed solution has proven to be an eminent success.
There are companies that everybody has heard of, even the people who don’t follow the Belgian industry sector. This is often due to an article in the newspaper or a report on the TV about a success story which illustrates the strength of Belgian companies abroad. You may remember the name Jan De Nul from the mega dredging project in Dubai or the new Suez Canal in Egypt. However, Jan De Nul Group is more than just a dredging company. They have four main areas of interest: dredging and marine works, offshore services, civil works and, finally,
environmental works. The JDN Group has grown into a global player by continuous investment into these four activities. In 2015 the group took over the foundation expert Soetaert NV in order to strengthen its expertise in hydraulic engineering and foundation building.
Unburdening its customers: Everything from design up
to execution is being taken care of
A success strategy is supported by many pillars but one of the most important ones is “unburdening the customer”. In the past, work was based mainly on following the customer’s specifications; today, customers are looking rather for a complete solution to their problem. The multidisciplinary teams of Jan De Nul Group follow the integrated approach – everything from design to execution is being taken care of with their own people and equipment. Some projects even include maintenance and financing. A customer always gets a creative and innovative solution tailored to their own specific needs. This endeavor is supported by a large design and engineering department which serves all four areas of interest.
Continuous investment into new technology and
equipment
An equally important part of the strategy is continuous investment into new technology and equipment. Let’s illustrate this by looking at JDN’s own fleet. It consists of more than 85 ships, 47 of which were built between 2007 and 2013. Bigger isn’t always necessarily better but for large-scale international projects that became JDN’s specialty, it is an asset that cannot be underestimated. The group works with world’s largest trailing suction dredgers, the sister ships Cristóbal Colón and Leiv Eiriksson with hopper capacity of 46 000 m³ and depth range up to 155 m, as well as the subsea rock installation vessels Simon Stevin and Joseph Plateau which are the most powerful vessels of their kind.
“We think that we can make complex parts best by
ourselves.”
More remarkably, Jan de Nul is one of the few dredger companies that design their vessels and equipment themselves. There are good reasons for this. “First of all you have better control over the delivery times and there is also the quality factor. We produce many complex parts of unusual shapes and that requires a great deal of know-how. We think we can make these complex parts best by ourselves. Furthermore, this knowledge you want to keep in your own house and not outsource,” says Jose Pycke, Workshops Manager for Jan De Nul Group. 70 operators work in the production department. It is divided into a material preparation area, welding workshop and machining workshop equipped for processing of very large parts. The largest vertical lathe can handle parts with a diameter up to 5,5 meters.
The complete cutting solution from MicroStep
“Our old oxyfuel cutting machine was still functional, but we couldn’t do weld seam preparation with it. We had to do the bevels manually with a hand torch or an angle grinder, and that took a lot of time. The machine from MicroStep solved this problem,” says Mr. Pycke.
“Furthermore, materials thicker than 25 mm had to be cut with oxyfuel technology which was much slower.” MicroStep delivered the complete cutting solution: with a
12 x 3 m cutting area for plates up to 150 mm thick and a zone for cutting pipes with a robot situated along the outer side of the machine guidelines, the machine is capable
of processing tubes up to Ø 2000 mm and wall thickness 80 mm. The challenge here was to ensure cutting and positioning of pipes in the entire required range of diameters
(Ø 100 – 2000 mm) and thicknesses and, at the same time, to propose a technical solution that would allow the most convenient manipulation of pipes while requiring
minimal construction interventions in the production hall. The final solution was an oxyfuel torch on a robotic arm, as this provides high movement flexibility and isn’t limited
by the height of the gantry. This way it was possible to place the pipe cutting tracks and supporting rollers on the floor level without the need to “sink it” underground. For
compensation of possible deviations of the pipe shape, a laser scanner integrated in the torch holder is used to scan the surface of the pipe in the place of the cut will be. If any deviations are detected, the cutting program is automatically adjusted. The use of a scanner in combination with a sophisticated robot movement control (compensating for the existing inaccuracies of the robot’s construction) and the dedicated 3D CAM software mCAM achieves accurate openings and contours of different shapes. The pipe cutting zone is equipped with a safety light barrier which turns on together with the robot to ensure operational safety.
“First of all, the plasma/oxyfuel cutting machine with the integrated robot has resulted in considerable time savings because all the weld preparation is now done automatically
and in one step, which also increases quality. As to the pipe cutting, not only has our reach been increased, but we can also cut any shape. In terms of flexibility, we have improved significantly,” José Pycke concludes.
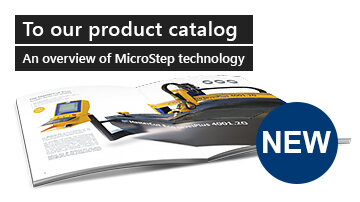
EXPERIENCE OUR SYSTEMS LIVE
in the CompetenceCenter South or North
- All four cutting technologies (laser, plasma, oxyfuel, waterjet)
- Innovative automation systems
- The latest solutions for bending and deburring
- Industry 4.0 demo factory
- Easy to reach: in the south and north of Germany
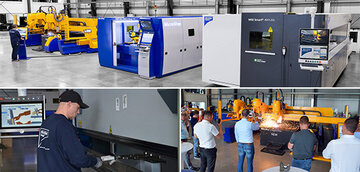