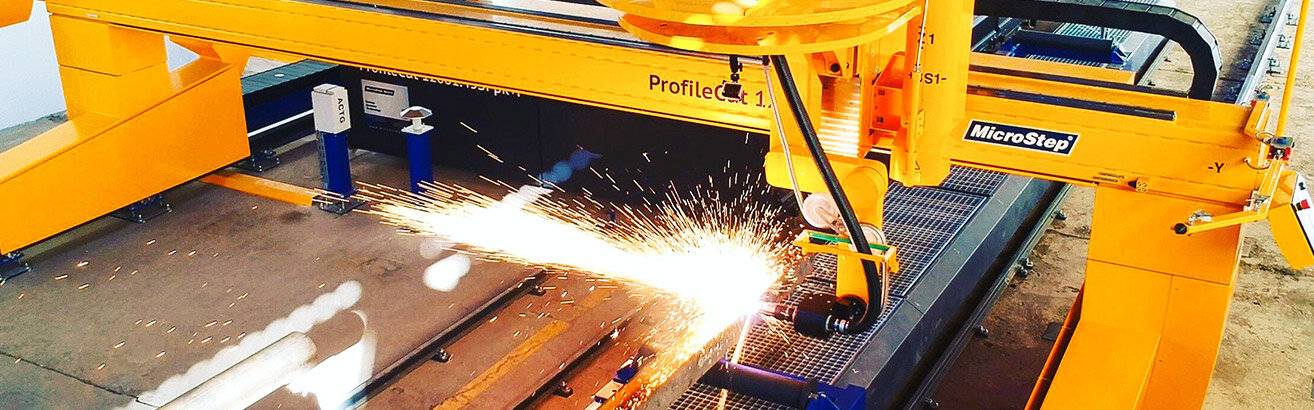
Bevel cutting of profiles, pipes and sheet metal: the flexible beam cutting machine ProfileCut with rotator "Pantograph"
Faster and better quality with new flexible cutting centre
The Spanish mechanical engineering company Innergy Heavy Industries relies on a multifunctional solution for 3D processing of beams, pipes and sheet metal
Published 23.11.2018 | Melanie Lingemann
Company profile:
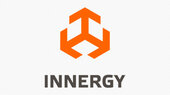
Avda. Juan Ramón Jiménez, 646930 Quart de PobletSpain
INNERGY is a multinational company specializing in eco-friendly energy solutions. It consists of three divisions (Innergy
Heavy Industries, Innergy Electric and Innergy Engineering), has three international headquarters (Spain, Chile and Japan)
and has worked on more than 6,500 projects on 5 continents so far. At the Heavy Industries factory, the company produces
everything from industrial burner boilers and biomass boilers to complete power generation plants.
Machine profile:
ProfileCut series- Working area for sheets 12,000 x 4,500 mm
- Cutting of H, I, U beams up to HEB 1000 and a length of
12,000 mm - Cutting of pipes Ø 30 – 700 mm and hollow sections up to a
length of 12,000 mm - 3D plasma rotator "pantograph" with tilting up to 120° for weld
preparation on beams, pipes and plates + auto-calibration
feature (ACTG®)
INNERGY is a multinational company specializing in eco-friendly energy solutions thinking not only about the needs of the customer, but also about the needs of our planet. When it was founded 50 years ago, the company has specialized in design and manufacture of thermal oil boilers. However, over the time the world has changed and Innergy had to change with it. Today, its portfolio contains biomass generation and cogeneration plants, boilers or systems for use of residual heat.
Today the company has three separate divisions (Innergy Heavy Industries, Innergy Electric and Innergy Engineering), three international headquarters (Spain, Chile and Japan) and has worked on more than 6,500 projects on 5
continents.
Innergy opted for the ProfileCut from MicroStep with a working area of 12 x 4.5 meters for cutting of flat metal sheets. The machine is equipped with a pipe positioner and supporting rollers for cutting of pipes with a diameter up to 700 mm and profile cutting zone for cutting of H, U and L profiles up to 12 m long and 600 mm wide. The "pantograph" rotator is capable of tilting up to +/- 90° which makes the profile cutting feasible. All this supported by the XPR300® plasma source from Hypertherm. Mr. David Moldes, Chief Strategy and Corporate Development Officer, shared the decision making insights in a short interview:
Since 2017 you use a sheet and pipe cutting machine. Why did you decide for the ProfileCut from MicroStep?
David Moldes: “Acquisition of new equipment in Innergy follows strict rules since we need equipment which meets high quality standards characteristic for our company. We aim to continue providing our customers with state-of-the-art industrial boilers and other products and with this in mind, we decided for MicroStep's ProfileCut. During the selection process we didn’t only take the machine’s features into account. The important factor was also the good references MicroStep has on the market.”
How has the machine helped your manufacturing process?
David Moldes: “Having the machine has helped us mainly in two areas. First of all, by reducing manufacturing times and at the same time by improving the quality of our heater products. In addition, thanks to the incorporation of the ProfileCut we no longer have to outsource the parts cutting. That gives us both speed and self-sufficiency.”
The Innergy company relies on the ProfileCut series - thanks to the plasma rotator "pantograph" with its tilting capability of ±90° (120° on one side), beams can be processed circumferentially. In addition, the plasma cutting machine enables the processing of pipes and sheet metal.
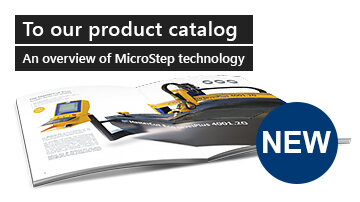
EXPERIENCE OUR SYSTEMS LIVE
in the CompetenceCenter South or North
- All four cutting technologies (laser, plasma, oxyfuel, waterjet)
- Innovative automation systems
- The latest solutions for bending and deburring
- Industry 4.0 demo factory
- Easy to reach: in the south and north of Germany
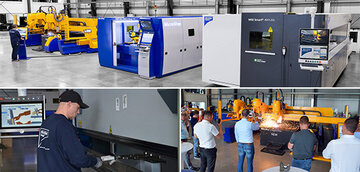